For the Processing of Shaft Parts, What Should We Consider?
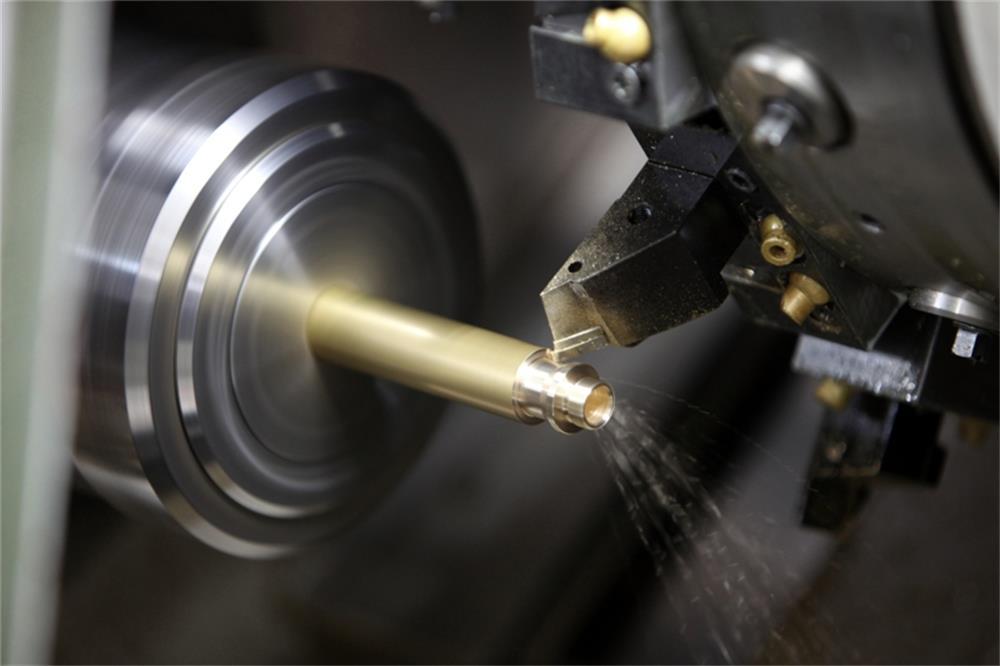
Shaft parts are a common type of machine parts, whose structure is a rotating body, and the length is generally greater than the diameter. They are widely used in various mechanical equipment to support transmission components, transmit torque, and bear loads.
Only by making the following sufficient preparations in advance, the shaft parts can be correctly processed by CNC or mechanical processing, so as to avoid errors in processing.
Process analysis of NC machining of parts drawing
(1) Whether the dimension marking method in the part drawing is suitable for the characteristics of CNC machining;
(2) Whether the geometric elements constituting the outline in the part drawing are sufficient;
(3) Whether the reliability of the positioning reference is good;
(4) Whether the required machining accuracy and dimensional tolerances of the parts can be guaranteed.
Process analysis of rough parts
(1) Analyze the adaptability of the blank in installation and positioning, as well as the size and uniformity of the margin;
(2) Whether the machining allowance of the blank is sufficient and whether the allowance is stable during mass production.
CNC Machine selection
Different parts should be processed on different CNC machine tools, so CNC machine tools should be selected according to the design requirements of the parts.
Selection of tool setting point and tool change point
Tool setting point: It is the starting point of the tool movement relative to the workpiece in exponential control processing.
Tool change point: It is set for the programming of multi-tool machinings such as machining centers and CNC lathes.
In programming, the workpiece is regarded as stationary, while the tool is moving. The tool setting point is usually called the program origin. The key points for selection are easy alignment, convenient programming, small tool setting error, and convenient and reliable inspection during the processing. The tool setting point should be coincident with the tool position point during the toolset.
Selection of processing method and determination of processing plan
The selection principle of the processing method is to ensure the processing accuracy and surface roughness requirements of the processed surface, but in the actual selection, the shape, size, and heat treatment requirements of the parts should be considered.
When the processing plan is determined, the processing method required to meet these requirements should be preliminarily determined based on the accuracy and roughness requirements of the main surface.
Selection of machining allowance
Machining allowance: The amount generally refers to the difference between the size of the rough body and the size of the part.
There are two principles for the selection of machining allowance, one is the principle of minimum machining allowance, and the other is there should be sufficient machining allowance, especially for the last process.
Determination of cutting parameters
Cutting parameters include depth of cut, spindle speed, and feed. The depth of cut is determined according to the rigidity of the machine tool, fixtures, tools, and workpieces, the spindle speed is determined according to the allowable cutting speed, and the feed rate is determined according to the machining accuracy and surface roughness requirements of the parts and the material properties of the workpiece.
For precision mechanical parts such as shaft parts, if the processing is to be carried out, fixed rules must be followed. If you want to know more about this after reading the above, you can get a comprehensive solution by contacting us.
As a professional parts supplier, we have advanced processing equipment and strict weight inspection, which can provide customers with high-precision processed parts. And we also provide thoughtful one-stop service, committed to providing customers with good solutions. If you want to buy our high-quality machine parts, please contact us immediately!